ISRO Successfully Tests a 3D-Printed Rocket Engine
On Thursday, May 9th, the Indian Space Research Organisation (ISRO) achieved a significant milestone by successfully testing a liquid rocket engine crafted with the aid of additive manufacturing technology, also known as 3D printing. This engine, named PS4, serves as the propulsion system for the fourth stage of the Polar Satellite Launch Vehicle (PSLV). ISRO ingeniously redesigned the engine to leverage the capabilities of 3D printing for its production.
What is 3D Printing?
3D printing, also known as additive manufacturing, is a revolutionary process that fabricates three-dimensional objects layer by layer using computer-generated designs. This method involves building up layers of materials such as plastic, composites, or bio-materials to create objects of varying shapes, sizes, rigidity, and colors.
How is 3D-Printing Done
To initiate 3D printing, all you need is a personal computer connected to a 3D printer. Designing a 3D model of the desired object on computer-aided design (CAD) software and pressing ‘print’ sets the process in motion. From there, the 3D printer handles the rest.
Unlike subtractive manufacturing processes, such as sculpting a statue from a single block of marble, 3D printing employs a layering technique. It builds objects from the ground up, adding layer upon layer until the final product matches the original design. In this process, a nozzle moves back and forth, depositing material layer by layer, similar to how a traditional inkjet printer works.
These printers can create a wide range of objects, from everyday items like balls and spoons to intricate moving parts like hinges and wheels. In fact, they have the capability to produce entire assemblies, such as a bicycle, fully assembled without the need for tools. This innovative technology opens up endless possibilities for manufacturing various objects with ease and efficiency.
Benefits of 3D Printing
3D printing offers a wide range of advantages over traditional manufacturing methods. Here are some of the key benefits:
- Rapid Prototyping: 3D printing allows for quick and cost-effective creation of prototypes. This enables rapid design iteration and testing, leading to faster product development cycles.
- Design Flexibility: Unlike traditional methods with limitations, 3D printing allows for highly complex and intricate designs. This opens doors for innovative and functional products.
- Customization: 3D printing can produce one-off customized items or small batches efficiently. This caters to personalized products and specific needs.
- Reduced Waste: 3D printing uses material only for the desired object, minimizing waste compared to traditional subtractive manufacturing techniques.
- On-Demand Manufacturing: 3D printing enables on-site or on-demand production, reducing the need for large inventories and complex supply chains.
- Lightweight and Strong Parts: 3D printing allows for the creation of lightweight yet strong parts using specific materials and printing techniques.
- Toolless Manufacturing: No need for expensive jigs or molds, making 3D printing potentially more accessible for smaller production runs.
Challenges of 3D Printing
Despite its numerous benefits, 3D printing also faces some challenges that hinder its widespread adoption:
- Limited Material Selection: While the range of materials available for 3D printing is growing, it’s still not as vast as traditional manufacturing. Some materials with specific properties are difficult or impossible to 3D print yet.
- Printing Speed and Cost: While printing times have improved, 3D printing of certain objects can still be slower than traditional methods. Additionally, high-quality 3D printers and materials can be expensive.
- Post-Processing: Some 3D printed parts may require additional finishing steps like support removal or surface treatment, adding to the production time.
- Strength and Durability: The strength and durability of 3D printed parts can vary depending on the material, printing process, and design. They might not always match traditionally manufactured parts.
- Design Complexity Limitations: While 3D printing offers great design freedom, there are still limitations related to overhangs, minimum feature sizes, and internal structures. Designing for 3D printing requires specific considerations.
- Intellectual Property Concerns: 3D printing technology raises concerns about copyright and intellectual property infringement. Easily copying designs could become an issue.
- Safety Regulations: As 3D printing evolves, standardization and safety regulations need to be developed for materials and printing processes, especially for applications in critical industries.
Why did ISRO use 3D printing to build the PS4 engine?
The utilization of 3D printing technology enabled ISRO to condense the engine’s components from 14 separate parts into a single piece. This advancement allowed the space agency to eliminate 19 weld joints, resulting in a remarkable 97% reduction in raw material usage. Additionally, ISRO achieved a significant reduction in overall production time, slashing it by 60%. Such enhancements highlight the transformative impact of 3D printing on streamlining manufacturing processes and optimizing resource utilization.
- RBI SO Syllabus and Exam Pattern 2025 for Grade A and B
- RBI SO Eligibility 2025, Check Qualification & Age Limit
- RBI SO Exam Date 2025, Check Phase 1 Schedule for Grade A/B
- RBI SO Apply Online 2025 Before 31st July for 28 Vacancies
- RBI SO Notification 2025 Out for 28 Vacancies of Grade A & B
- Free SSC CHSL Topic Wise Tests for English, Quant & More, Attempt Now
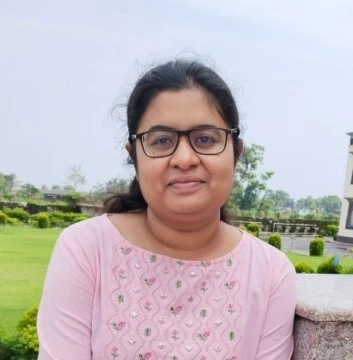
Hello, I’m Aditi, the creative mind behind the words at Oliveboard. As a content writer specializing in state-level exams, my mission is to unravel the complexities of exam information, ensuring aspiring candidates find clarity and confidence. Having walked the path of an aspirant myself, I bring a unique perspective to my work, crafting accessible content on Exam Notifications, Admit Cards, and Results.
At Oliveboard, I play a crucial role in empowering candidates throughout their exam journey. My dedication lies in making the seemingly daunting process not only understandable but also rewarding. Join me as I break down barriers in exam preparation, providing timely insights and valuable resources. Let’s navigate the path to success together, one well-informed step at a time.